Why do some drivers experience a vibration through the steering wheel or the brake pedal during braking? Why do brake discs turn blue or crack?
Physics of braking
First, some theory. When braking, the brake pads are pressed against the brake disc and cause friction. In this case, the brake disc heats up as the kinetic energy created under braking is converted into heat.
Another function of the brake disc is to dissipate the heat generated during braking. The friction material of the pad contains abrasives that interact with the surface of the disc - one unevenness clings to another. Adhesive friction also appears, in which one surface tends to stick to another.
It is important to keep in mind these two phenomena during braking.
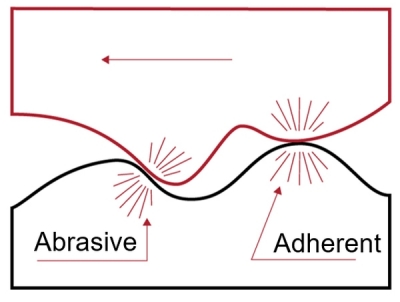
Types of friction during braking
1. Brake Discs Overheating
The first cause of brake disc run-out is overheating. Overheating is destructive. The cast iron structure of a standard brake disc begins to change when the critical temperature of around 650°C is reached. This temperature is easily exceeded if the driver does not allow the discs to cool down after repeated sudden braking from high speed. Also, overheating of the brake disc can be the result of excessive friction due to improper bedding-in of the new pads.

An overheated brake disc
The amount of energy released during one braking instance from a speed of 90 km/h is enough to boil two litres of water in three seconds. In the case of a truck, this energy is enough to boil 53 litres of water in 4 seconds.
With intense braking, the temperature of the pads and discs can reach 500-550°C. A further increase in temperature is fraught with a decrease in braking efficiency. If the temperature reaches the critical point of around 650°C, the surface of the disc changes its crystalline structure and the cast-iron structure turns into a much harder phase called cementite. At the same time, in the inner layers of the material where overheating has occurred, the cast iron retains a softer structure.
The combination of soft cast iron and hard cementite creates an ice crust effect. Cementite has a lower coefficient of friction compared to cast iron, so the block pressed against it will slip relative to another part of the disc surface. The result is uneven braking, which is clearly felt on the pedal. In this case, the runout of the disc will not always exceed the critical values, which are not more than 0.1 mm along the outer periphery of the disc.
The structure of a normal disc, consisting of grey cast iron, and the modified structure of cementite, differ markedly when viewed under a microscope. The cementite crystals on the surface look like ulcers on the surface of the brake disc. The first visual signs of local overheating may be clearly visible blue spots on the disc surface.
Blue spots on the brake disc surface
Intensification of extreme overheating leads to further propagation of the crystalline structure of cementite on the surface of the brake disc, causing a change in its geometry. The disc drives and the driver feels the run-out.
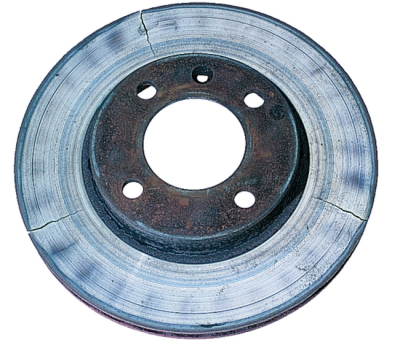
Cracks on the brake disc operating surface
The length of cracks should not be more than 25-30 millimetres. The longer the crack, the deeper it is, which also affects the disc geometry and the likelihood of run-out. Overheating of the disc, which may not be visually noticeable, can be indirectly determined by white crumbling edges of the pad.
Solution
Follow the rules of bedding in the brakes – during the first 300km it is important to brake moderately. Heavy braking should be avoided in the bedding-in phase otherwise the discs will not have time to cool down and could potentially reach a critical temperature at which the risk of overheating increases considerably.
Keep the caliper guides clean. If they are acidic or rusted, the caliper may not open, and the pads may not move away from the disc surface. Friction in this case will be constant and the disc will overheat.
2. Worn-Out Discs
Also, very often the disc overheats or cracks because it is worn, and replacement is long overdue.
Minimum brake disc thickness
Many people believe that the brake disc must be replaced when its thickness has reached the minimum value, regardless of the thickness of the brake pads.
Another point of view allows the use of a brake disc with a minimum thickness in conjunction with new brake pads. As soon as they wear out, you can put new discs and pads. This is incorrect and is not safe.
Those who change the disc when the minimum thickness is reached are doing the right thing.
The recommended minimum brake disc thickness is based on physics. If the thickness is insufficient, the disc cannot dissipate the heat that is generated during braking. It also cannot maintain the required strength. The temperatures are significantly higher than permissible and there is a high risk of overheating and even physical destruction. Also, a worn-out brake disc is more prone to resonance effects causing brake noise.
New brake pads cannot improve this situation. The service life of a worn brake disc is less than that of new brake pads. If the disc thickness is within the specification, but close to the minimum allowable value, then it must be replaced when installing new brake pads.
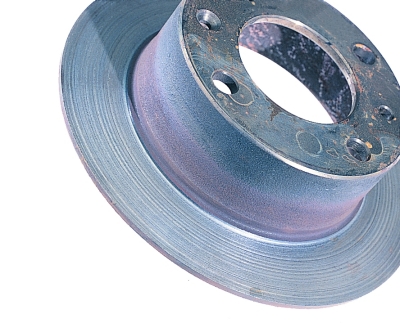
Brake Disc heavily worn with surface grooves
3. Dirt between the hub and brake disc
The third problem, which is often forgotten, is the contamination of the hub surface and the inner surface of the brake disc. A layer of rust may not be obvious but just 2-3 grains of sand on the hub and it is already 0.1-0.15 millimetres at the outer radius leading to a noticeable run-out. If there is dirt on the hub, either clean or change.
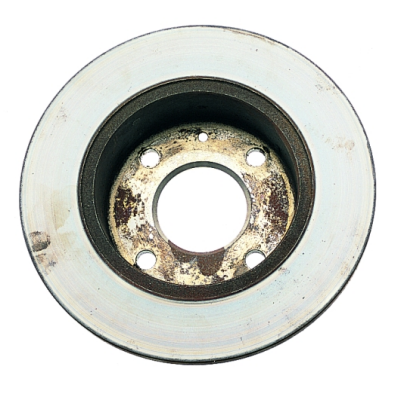
Disc surface contamination
Solution
When replacing a brake disc, it is important to thoroughly clean the surface of the hub. A small grain of 0.05 mm is enough to start feeling vibration on the steering wheel. In a disc braking system, the average clearance between the pad and disc surfaces is around 0.1 mm. A grit of 0.05 mm on the hub gives 0.1 mm on the periphery and leads to contact between the pad and disc while driving. This may lead to noise when braking.
4. Brake disc thickness variation
The fourth reason for brake disc run-out is unevenness in the thickness of the disc. The reason for this is the uneven transfer of pad friction material to the disc surface. This often occurs when brake bedding-in instructions are not followed. A misaligned brake disc can also cause Disc Thickness Variation (DTV).
In order to understand that the thickness of the brake disc is uneven, it is necessary to measure it with a micrometer in 8 zones around the circumference of the disc with an interval of 45 degrees at each point. The outside, middle and inside of the disc should be measured. This method of measuring the brake disc allows you to determine the brake DTV over the entire working surface.
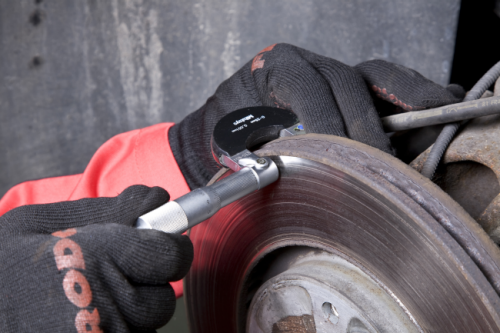
Measure the disc with a micrometer in 8 zones
From all obtained values, the minimum and maximum are selected, after which the difference between them is calculated. Let's consider the spread of values between 0.025-0.035 mm. This is enough to measure the thickness of the new disc at three points, and then it should be checked against the parameter specified in the installation instruction for the disc. Information on the maximum permissible minimum thickness should be found in the recommendations from the car maker, or on the edge of the disc itself.
Check this video to learn how to measure brake rotor thickness.
5. Incorrect installation of the brake disc
Brake disc run-out can be caused by a skewed seating relative to the hub, which in turn may be the result of contamination of the seating surface or deformation. Another cause of misalignment is wheel bearing play or caliper misalignment.
The distortion of the contact surface with the hub is caused by excessive or insufficient tightening of the wheel bolts or nuts, as well as non-compliance with the tightening torque and sequence recommended by the manufacturer. Other causes are overtightening of the wheel bolts or nuts, mechanical stress from displacement, and improper assembly or installation of the caliper and disc. The consequence can be noise, vibration or even disconnection of the contact surface from the hub.
Solution
Replace the disc with a crisscross pattern and torque according to the manufacturer's recommendations. Before installing the discs, you should check the correct assembly and installation of the calliper housing.
6. Brake disc quality
Poor quality brake discs cannot always be recognized by their appearance. The main reasons are the quality and composition of the material, non-compliance with the production technology or the use of outdated technologies.
Solution
Avoid cheap parts of unknown origin and instead choose quality brake discs from well-known manufacturers.
Ferodo brake discs are produced using only the best metallurgy, the highest quality casting processes, Original Equipment levels of construction and strict quality control measures. All tested and approved by Ferodo engineers who develop braking solutions for the brake systems suppliers and vehicle manufacturers.
Remember
- Change brake discs as soon as they reach the recommended minimum thickness.
- Choose quality brake discs, avoid products of unknown origin.
- Use a qualified technician to ensure that the brake disc is fitted correctly.
- During installation, ask a specialist to service the brake calliper.
- After installation, take care to bed the brakes in by braking lightly and often, for the first 300 km.
For more info on brake disc failures, please check the brake disc trouble tracer:
The content contained in this article is for entertainment, informational and promotional purposes only and should not be used in lieu of seeking professional advice from a certified technician or mechanic. We encourage you to consult with a certified technician or mechanic if you have specific questions or concerns relating to any of the topics covered herein. Under no circumstances will we be liable for any loss or damage caused by your reliance on any content